Still on a quest to unlock more colors on my FDM printer. (instagram.com/nozzleboss)
It's a passive mixing nozzle that can evenly coat one filament with another filament.
Different mixing ratios allow you to vary the coating thickness of the extrusion and change the color continously. (In theory only limited by the step resolution of extruder motor.)
2 blue inlets from the side coat the white core (3 extruders total)
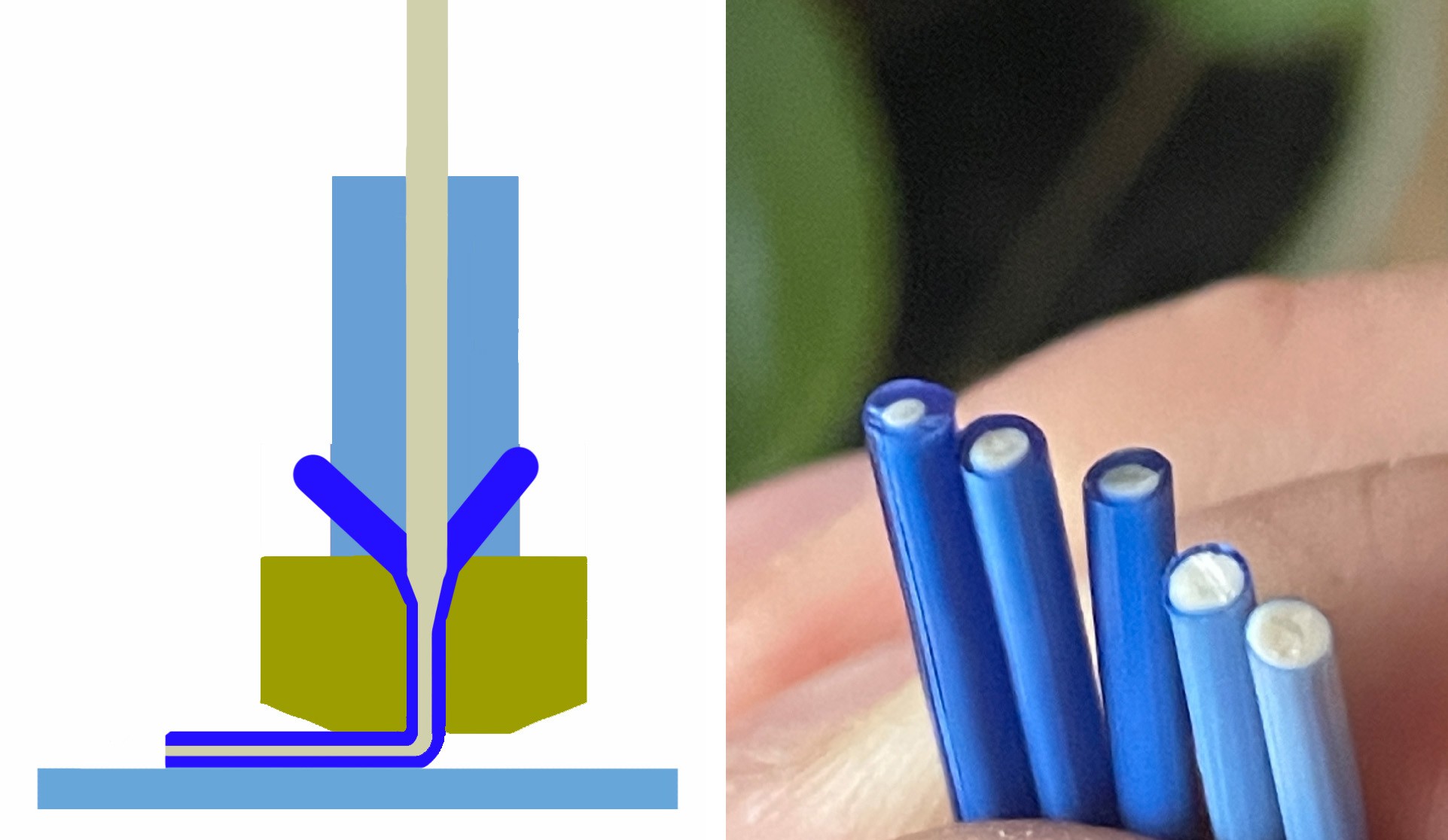
This avoids the toothpaste effect of other passive mixing hotends and lets you print very smooth gradients.
On the software side I've been using my nozzleboss addon for Blender to map vertex colors to different mixing ratios. This way you can paint a grayscale texture in Blender onto the G-code paths and the texture value gets converted to the correct mixing ratios/coating thickness.
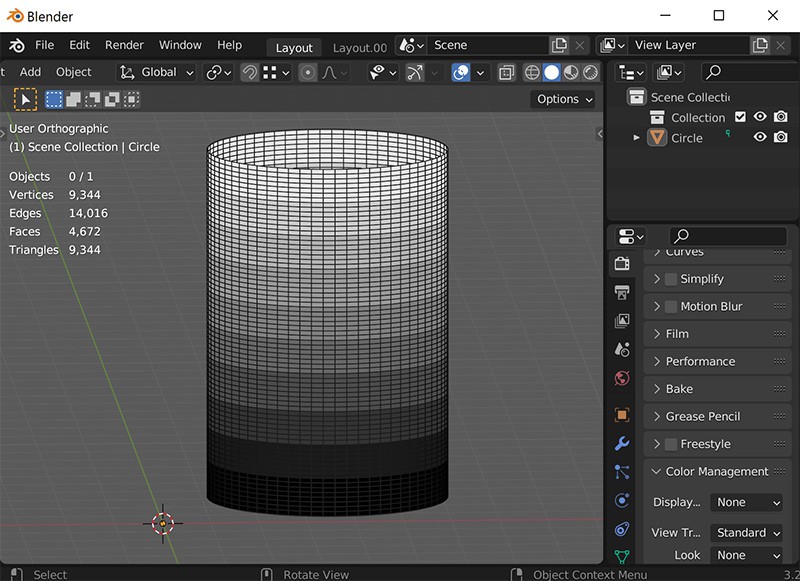
Version 2:
I tried printing the hotend in aluminium and added a 4th color channel.
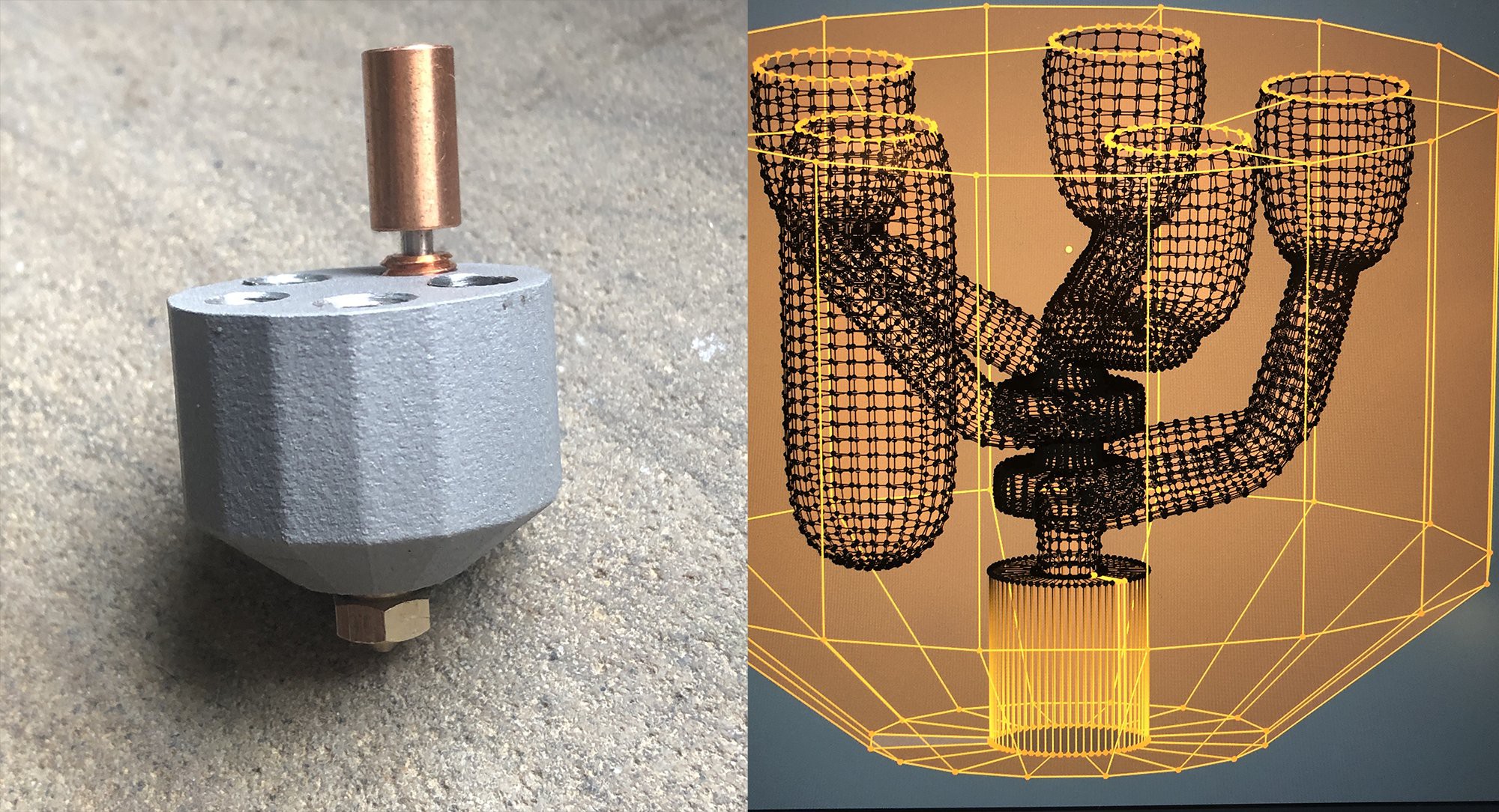
First printing tests with the new nozzle and two additzional color channels:
Version 3 (5 color channels):
Resin print shows the inner workings of the coating nozzle. (testing with acrylic paint here)
Yellow and red both are coating colors (toothpaste effect, since they share the same output)
White is a core color and can be mixed with red to get continous tones.(2nd part of video)
Nozzle has 5 color inlets overall (2 core colors, 3 coating colors)
Each coating color branches out into four separate channels to evenly cover all sides of the core color.
The transparent version 3 looks very nice.
1) Has the design also being printed in metal, or are you testing it in resin first so that it can be optimised beforehand?
2) Hypothetically, could an off-centered inlet approach improve coating performance? See [https://youtu.be/3sp91_g48jA?si=_ranJF1kadeDl4fQ&t=333] to show what I mean. This log [https://hackaday.io/project/190831/log/222620] is the project log I've written to further explain my hypothesis.