Oasis
Oasis is a open source powder and inkjet (3DP) 3D printer. It is designed to be a hackable platform to experiment with 3DP printing.
Current specs:
- Build size: Ø84mm x 100mm;
- Printhead: HP45;
- Printhead DPI: 600;
- Printhead swatch size: 300 nozzles, 0.5" (12.7mm);
Handy features:
- A cover to keep dust out and powder in. (This may seem mundane, but was seriously lacking in my previous printers).
- A large, flat, unobstructed build area that is easy to clean. (Again, seems mundane, is not mundane).
- An aluminium extrusion frame where parts can easily be bolted on.
- Plenty of room for future additions (It should be able to handle 5 printheads or a 200mm cubed print area).
Logs of interest
- https://hackaday.io/project/86954-oasis-3dp/log/117820-a-bit-of-background
- https://hackaday.io/project/86954-oasis-3dp/log/118433-an-introduction-into-3dp-and-oasis
- https://hackaday.io/project/86954-oasis-3dp/log/123969-a-start-on-the-inkjet-controller
- https://hackaday.io/project/86954-oasis-3dp/log/145601-construction-in-progress
- https://hackaday.io/project/86954-oasis-3dp/log/153322-some-info-on-interfacing-with-the-hp45
- https://hackaday.io/project/86954-oasis-3dp/log/153411-the-color-of-the-day-blue
How 3DP
'3DP' also going by the names 'binder jetting' or 'powder and inkjet printing', is a technique that uses inkjet and powder to fabricate parts. 3DP printers consist of a moving inkjet printhead, a build area, and a way to deposit new layers of powder in said build area. The example below uses 2 hoppers and a spreader. The left hopper supplies the powder and is called the 'feed hopper', the part is built in the right 'build hopper'. A spreader can move between these hoppers to transfer powder from one to another. The order of operation for 3DP printing is as follows:
- The inkjet head deposits binder wherever the part needs to be. Where the binder fills the powder, the powder solidifies;
- The build piston lowers by the layer thickness, the feed piston raises enough to fill the build area completely;
- The spreader spreads the powder from the feed hopper to the build hopper;
- The spreader returns and the printer starts at step 1 again. This is repeated until the part is finished.
After this printing, the part is allowed some time to dry. It can then be removed from the printer and gently cleaned. After this the part can either receive further processing, or be used directly.
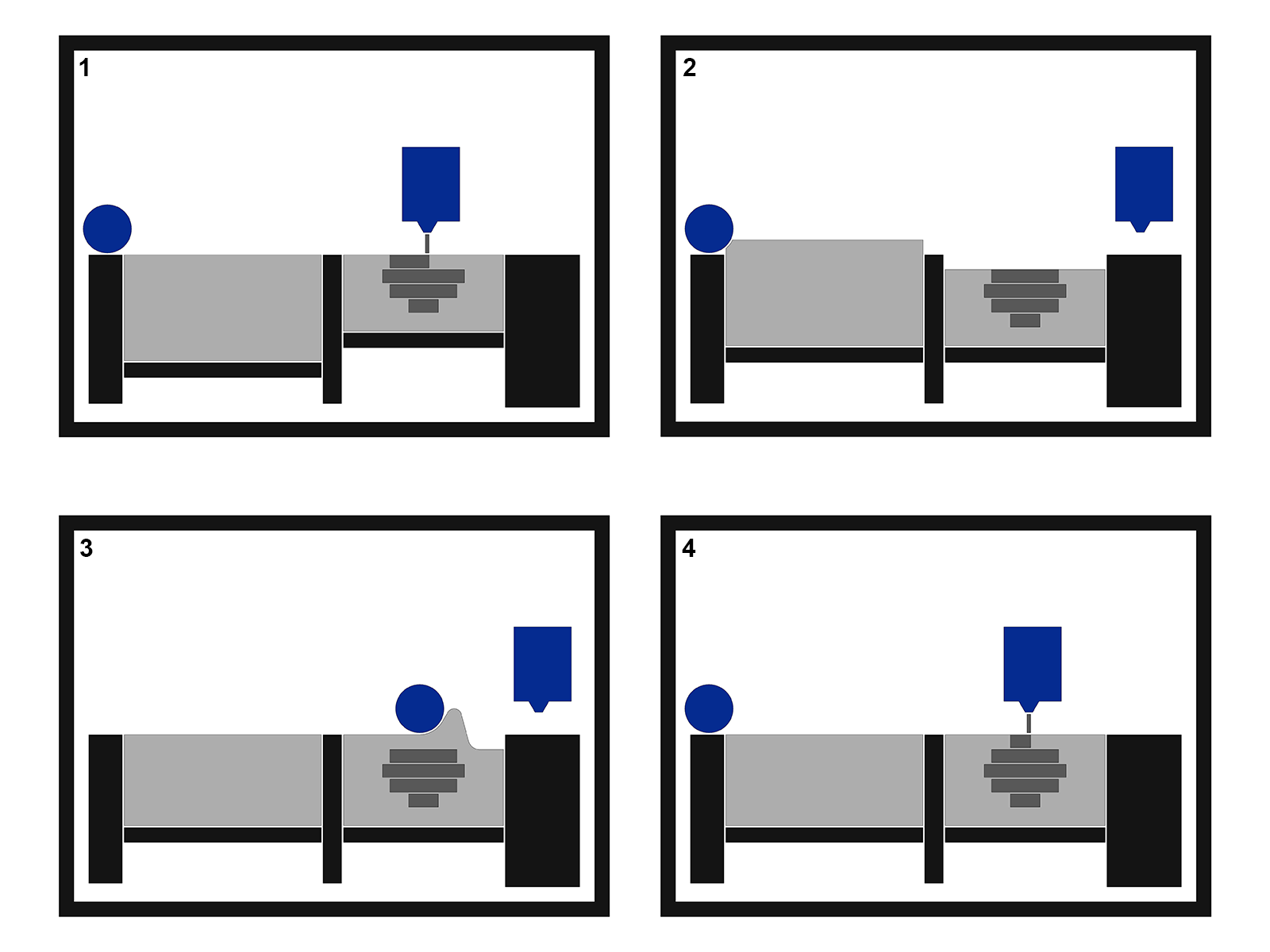
Why 3DP
3DP is quite unlike FDM and SLA. It's biggest advantages are:
- You do not need support material. The powder is added one layer at a time, and the powder from the previous layers supports the next layers. All the unprinted powder can be reused infinitely.
- A wide range of materials can be printed. While FDM is limited to plastics, and SLA requires light sensitive resins, 3DP can print most materials that come as powders.
- Color can be printed. Because 3DP uses standard inkjet technology, it is possible to add color, simply by printing dye alongside the binder.
3DP is not perfect though, There are some drawbacks that need to be considered:
- Powder printing is inherently messy. Very messy.
- All prints require post processing, ranging from simple cleaning to firing or infiltrating. Untreated parts are very fragile. This also limits maximum size of parts. The part needs to be able to survive post processing.
- All of the print area needs to be filled with powder. While the excess can be reused, a minimum amount of powder is required to print at all.
- 3DP prints only one material at a time.
- Hollow parts need escape holes to drain unprinted powder.
What 3DP
There are a variety of materials 3DP can print. The only thing these materials have in common is that they are powders. In most cases, a glue is added to the powder. Examples of this are PVA, sugar or maltodextrin. The binder is generally an inert liquid, like an alcohol/water mix. I have...
Read more »
Hi there,
I have some software problems as follows, and hope to get your suggestions:
1. I changed the size of the printer and I just wondered can I just adjust the related dimension parameter in the controller software part without modifying the firmware.
2. When I tried to print, the "BWL" value will decrease from 999 to 50 with the printing of several layers and stopped printing. I wonder how to solve this problem.
3. The "Prime" function works well but the printer head always did not inject inks during printing.
Best,
Aaron